What are fishbone aisles?
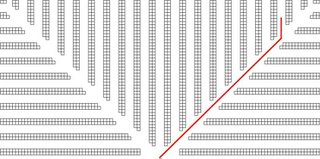
Fishbone aisles comprise a new design for unit-load warehouses that significantly (on the order of 20%) reduces the expected distance to travel to make a pick or stow. The idea is a simple one: Imagine a warehouse with single-deep selective rack having a single pickup and deposit (P&D) point at the bottom center. Each pick or stow begins and ends at the P&D point. The "spines" of the fishbone aisles extend diagonally from the P&D point with "bones" radiating from them, at appropriate angles.
The idea is to approximate travel "as the crow flies," which would be straight-line distance from the P&D point to the picking location. This cannot be done, of course, but a little thought and experimentation with the figure above should convince you that fishbone travel is very close to "travel by flight." By contrast, a traditional warehouse forces rectilinear travel (travel at right angles), which is far from optimal.
Our mathematical models suggest that, for typical warehouse sizes in industry, expected distance to make a pick in a fishbone warehouse is about 20% lower than for a traditional warehouse.
Your thoughts?
- What issues do you see with such a design in practice? (Please read my post on Modeling Assumptions before responding.)
- Congestion concerns? How might they be handled?
- We have thought about worker disorientation --- might they simply get lost?! Keep in mind that we assume they are going to store or retrieve only a single item.
- Construction issues? Spacing of building columns has been mentioned at some of our presentations. Why couldn't the columns be built around the racks, instead of the other way around?
--Kevin
6 Comments:
Comparing fishbone to V-shaped layout: Fishbone eliminates safety concerns of larger-than-90° turns, as in an unit load warehouse with single picks per visit no turns will be larger than 90°! However, worker orientation may be an issue. In V-Shaped, as all aisles are parallel, rack location may be (hypothesis would have to be proven) easier to recall (without aid of warehouse routing softwares). In fishbone, change of sequence and direction can cause worker to lose reference, but this negative effect could increase exponentially in case or less-than-case picking environments, where multiple picks per route (MPPR) are necessary. Zone batching schemes for MPPR environments could reduce this effect.
The fishbone design has real possibilities. The concern I see working as I do in a DC-
The single P&D is a heavy congestion point. Handling both inbound and outbound.Supposing a 3% increase in required storage space to make the design effective,
one would want to maximize the current floor space to this design.
How is it factored in for staging areas of inbound and outbound? Yes we can use the design to a set boundary, allowing for the area of staging. Will this lessen the storage space? Using the design wall to wall in an existing situation, I can begin to see the benefit. As a subset design inside an existing situation, I am not so sure.Still the congestion point is an issue for the forklift traffic, foot cart traffic,what have you. This design can lend well to "zoning" however.
Perhaps you could cut down on the disorientation of workers by posting small maps periodically along each aisle. A worker could have an instant grasp of there exact location with a single glance. Sounds cheesy but a simple top down veiw of the warehouse layout with a small red "you are here" dot could be quite effective. You could also cut down on the congestion at the P&D by making this area slightly larger with say a half moon shape entrance.
These are both solid suggestions.
I like the fishbone design. I think it's a good idea in small products, same size products and perhaps a
"start-up" building. For heavily mixed size product or conversion of existing layout, it may be too much to deal with.HMMM.
if this is a warehouse layout how does the practice bear up on high bay warehouses where the cross aisles are bridges rather than clear openings to the roof. ie where the cross aisle is simply the first beam level omitted and the forklift passes underneath.
it seems to me that any gain in travel times would be negated by a loss of storage capacity. is this factored in?
Hey I’m Martin Reed,if you are ready to get a loan contact.Mr Benjamin via email: lfdsloans@lemeridianfds.com,WhatsApp:+1 989-394-3740 I’m giving credit to Le_Meridian Funding Service .They grant me the sum 2,000,000.00 Euro. within 5 working days. Le_Meridian Funding Service is a group investors into pure loan and debt financing at the returns of 1.9% to pay off your bills or buy a home Or Increase your Business. please I advise everyone out there who are in need of loan and can be reliable, trusted and capable of repaying back at the due time of funds.
Post a Comment
<< Home